Senior recurve engineer George Tekmitchov explains the relationships between arrow spine and weight, and how to decipher your arrows’ weight codes
When it comes to finger shooting recurve bows, there is no more important arrow specification than arrow spine. Consistent, correct arrow spine for each and every arrow shot from a particular setup is paramount to grouping performance. The reason is simple and obvious if you have ever seen the behavior of an arrow shaft leaving a recurve bow. All of a shooter’s arrows must bend in the same manner on every shot, shot to shot, in order to group.
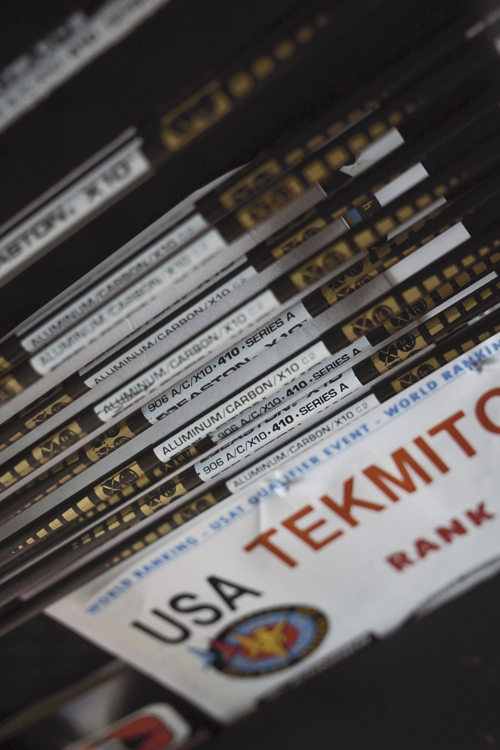
The two lines of numbers on an X10 shaft reveal important information about the arrow’s construction
While most accomplished archers know this intuitively, I once undertook a project to determine exactly how spine tolerances affect score. After all, when it comes to target archery, score is all that really matters. In the 1990s, I arranged a test in which American archer and Olympic medalist Denise Parker shot a specific dozen arrows every day for a six week period, carefully documenting every single shot and its impact point on the target at 70 metres. Half of the arrows Denise was shooting were properly matched in spine, while the other half were at a tolerance used by a non-Easton shaft. The shafts were blind coded and mixed, and visually identical, so Denise had no idea which ones were which. At the end of the six week study, all of the data were examined, and we found that there was a two point difference in raw score for every 12 arrows shot – the same two point margin that decided 80 per cent of the World and Olympic matches of that era, and still decides most sets in the current competition match format. It might seem obvious how important spine is, but there is nothing quite like real-world proof to see just how important.
If you have ever looked at a set of premium Easton A/C target shafts – X10, Pro Tour, ACE, ACC, ACG, or Pro Field – you may have noticed a somewhat mysterious code on the labels; “C2” or “C3” or “DP” or some other combination. This is what Easton calls a Weight Code. The purpose of this article is to explain what these weight codes are, why they’re important, and what you need to know about them.
I know I started talking about the importance of spine, and you’re probably wondering how that relates to weight, but I’ll get to that shortly. In order to understand weight codes, first you must know a bit about the materials used to build arrow shafts. Specifically, you need to know a little bit about how the stiffness-to-weight of a given material is expressed. Engineers use a dimension known as Young’s Modulus of Elasticity, usually simply referred to as ‘elastic modulus’, to express this property.
All experienced shooters know that when it comes to pure consistency, there’s nothing better than aluminum as a shaft material. Within a given alloy, the stiffness to weight ratio of an aluminum arrow is amazingly consistent. As long as the dimensions of wall thickness, diameter (inside and outside) and concentricity are spot on, the stiffness (spine) of the arrow will also be spot on. The reason is simple. Aluminum alloys have extremely exact elastic modulus values from one arrow production batch to another. For example, XX75 alloy is always very close to 10,400,000 million modulus, whether it was made in 1964 or last week. The stiffness to weight, and the spine of a given size XX75 arrow will always be exact because all 7075 aluminum alloy has this exact stiffness to weight property.
Not so with carbon fibre. Commercial carbon fibre can vary by more than plus or minus two million modulus, which is a relatively huge amount. For instance, one typical fibre used in premium carbon shafts has a modulus of 46,000,000. But, unless an arrow manufacturer takes the extra steps needed to improve upon the normal material variation, this could range from 44,000,000 to 48,000,000, or more.
An additional variable is found in the epoxy or other polymer resins used to hold the actual carbon fibres together in the arrow shaft. The percentages of resin to carbon must be held to a very tight tolerance to keep this under control and produce a structure that has a consistent ‘bulk modulus’ – that is, the stiffness of the combination of materials, in this example, epoxy and carbon fibre, which is something all carbon fibre composites have in common. But the ratio is subject to variation from several process and material related issues. Even the age of the starting material can have a tremendous effect on the stiffness properties, because this factor affects several process-related variables that can alter the outcome.
Any single one of these variables can substantially affect the stiffness of the arrow. Combine the variables that are possible, and you can see that some shafts can have a tremendous spine variation.
This is so important for accuracy that Easton takes several important steps to mitigate the effects of these variations. First, as the largest carbon buyers in the archery industry, Easton works directly with the companies who make the carbon fibre to obtain only select material lots, which are as close as possible to the exact stiffness needed for a given design. Using only select materials from the world’s premiere carbon fibre manufacturers, and continually testing the materials as they are prepared for use, minimises most of the carbon fibre variation. Another important factor is that Easton does all of the arrow fabrication. From the construction of the super-precise aluminum core and accompanying preparation to the carbon wrapping, curing, machining, straightening, and other finishing operations, Easton carries out each step entirely in its facilities in Salt Lake City, USA. This ensures total control over all of the many processes and steps required to create each arrow shaft.
Still, even using the finest carbon fibre available, and precisely controlling the other variables is not enough to completely eliminate the variation. There are two approaches to dealing with this issue.
First, you could simply finish the arrows to a given weight, and allow the spine value to float. This would result in the performance problems mentioned at the beginning of this discussion.
The second way is that you could construct arrows to the exact spine needed, as that is the most important consideration for arrow shaft accuracy and consistency, especially for finger release. This is where the importance of weight codes comes into play. Easton produces every arrow to the precise spine specification required, and then takes the additional step of individually weighing each shaft and assigning that shaft to a group – known as the weight code group.
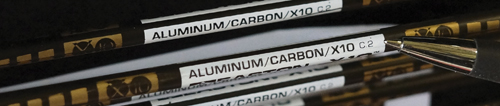
C.2 denotes the weight code on this arrow, and there is typically less than a one-grain increment between weight codes
If you look at the label of an Easton X10 shaft, you might be a little bewildered by the various numbers and codes indicated. First off as shown in the photo, there are two separate lines:
906 A/C/X10 410 Series A
Aluminum/Carbon X10 C.2
Looking at the numbers in order: 906 is the core tube size expressed as diameter and wall; 9/64ths diameter and 0.006” wall thickness. All X10 sizes are based on this size core tube, so all use the same basic components.
A/C/X10 is the model designation. 410 is the spine value, which relates to 0.410” deflection per ATA standard.
Series A is the design revision for that particular size shaft. A is the first production series (dating to 1995 when I first designed the X10 shaft). In case of any changes to materials or other specifications over the years, a separate series is issued.
On the second line is the weight code. In the case of my specific arrows in the photo, you can see the designation C.2. When a production run (of thousands of arrows) is created, each arrow shaft is weighed after final spine-tuning, and the entire population of arrow shafts can be charted (as with a bell curve) for weight. Typically, there is about a five to six grain total spread from lightest to heaviest among the thousands of arrows in a given run of a given size, and this is subdivided into less than one grain increments for assignment to a specific code.
- All ACE and X10 weight codes cover a total spread of 1.5 grains (.097 gram)
- All packaged shafts are +/- 0.5 grains in that package
- It is easily possible to mix shafts from two adjacent weight codes with no ill effect (‘heavy’ C.2 and ‘light’ C.3 for example)
Spine is so important to arrow accuracy that Easton goes far beyond the rest of the industry to ensure that you receive both the specified spine and matched weight for every premium target shaft produced in a given model. Weight codes are one of several methods used to ensure that every premium shaft you purchase of a given size and code will correctly match those you already have, or will obtain in the future. This is one of the more significant reasons why weight-coded shafts have won every Olympic podium since 1996.
Hi Nicola,
very helpful article. Well done – and very helpful.
A question, a story, and a suggestion:
Question: when you say “All ACE and X10 weight codes cover a total spread of 1.5 grains (.097 gram). All packaged shafts are +/- 0.5 grains in that package” – do you mean that if I buy a sealed tube of 12 ACEs their weights could range over 1 grain and still be in spec? I.e. “+/- 0.5 grains” means 0.5 grains either side of the median.
The story: I ask the above because I recently bought 24 brand new ACE 670 C3 shafts in two new tubes, all cut (by Quicks’ saw) from the same end to exactly the same length. Initial weighings, straight from the tube, were all a bit different, so I cleaned the internal ends to get rid of any saw residue, and gave the inside a blast of compressed air to flush out any dust etc. Then I weighed them again carefully. My grain scales read to 0.1 grains, but the repeatability is around 0.3grn – so I weighed every shaft five times (in random order), all balancing on exactly the same point, and averaged the readings.
The result was a big surprise:
– the first dozen ranged from 164.3grn to 166.0grn (range of 1.8grn i.e. 1.1%)
– the second dozen ranged from 164.2grn to 165.6grn (range of 1.4grn i.e. 0.9%)
I think I’ve allowed for any repeatability error in my scales. So can it be that Easton’s quality control on ACE shafts of +/- 0.5grn is not actually what is delivered?
BTW, I got 14 brand new 100 grain Easton break-off points here. I weighed them all as per the procedure I used for the shafts.
The result was a another surprise. Again I was expecting all their weights to be be very close, maybe +/- 0.3 grains or so. But they ranged from 99.3grn to 100.2grn (range of 1.0grn i.e. 1.0%!!!)
So… lots of matching-up going on here to end up with completed arrows all within a range of 0.5 grains.
The suggestion: point out the reason for worrying about weight variations: some senior coaches at Archery GB told me 7 grains would mean 2 colours at 80-90m (now everyone believes this…). I cater for wear over time by random selection of arrows and occasional weighing, but best to start out as close as possible.